Zeeman
3 min leestijdZeeman TextielSupers transforms its location and supply chain to realize growth ambitions.
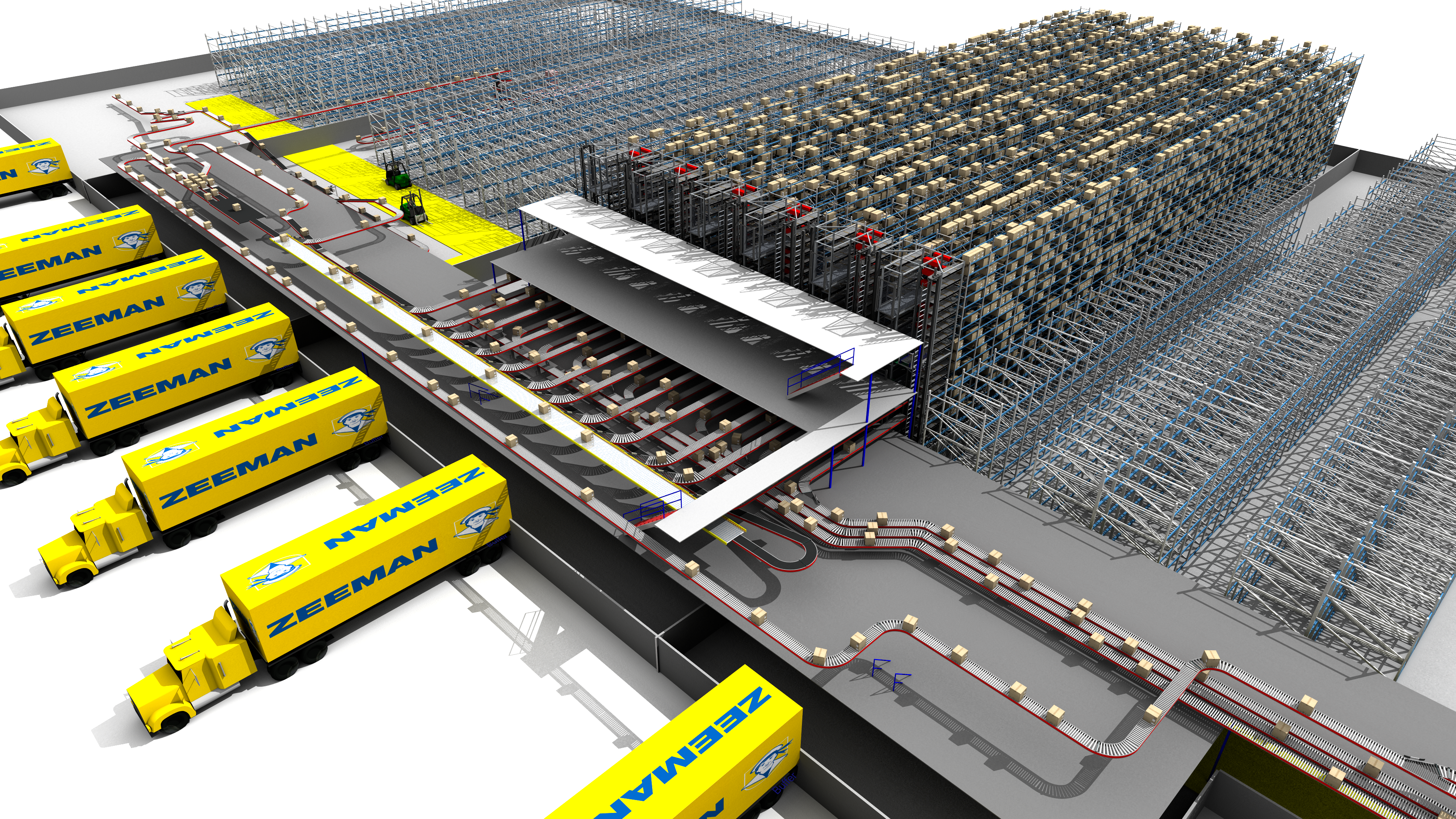
Working closely with Zeeman's management, we translated the executive team's growth ambitions into concrete impacts on the supply chain and logistics. The logistics center in Alphen aan den Rijn needed to support these growth ambitions and enhance product availability in stores. Our comprehensive support for the Zeeman team encompassed developing a functional design, selecting a system integrator, designing the layout, and managing the implementation of the facility renovation, mechanization, and the new Warehouse Management System.
Various strategic questions
There were several strategic issues impacting the supply chain over time. The first question was whether the current distribution center could support the projected growth. The shareholders and management preferred to remain in the existing facility if possible. Our answer was affirmative, albeit with conditions: either through extending operating hours or implementing mechanization. The follow-up question concerned the feasibility of a business case for mechanization, with a cross-docking approach instead of traditional storage. Once it was demonstrated that significant reductions in both storage and labor were achievable, the sales team inquired if the mechanization could also enhance inventory availability in stores.
Mechanization Choice
Given the complexity of the mechanization involving various processes, it was decided to outsource the mechanization to a system integrator. The tender process followed the traditional steps: longlist, request for information, shortlist, and ultimately selecting between two concepts. We conducted an in-depth evaluation with the developers of these concepts, which led to the selection of Inther and their shuttle concept.
To explain this decision: Zeeman has a limited fixed assortment and delivers a small number of new items in bulk twice a week, resulting in a limited number of high-volume logistical units. A mechanized flow rack system with high input and output would have been ideal for cross-docking and could have replaced the outdated sorter system. However, this solution would not have supported the goal of increasing inventory availability, as it could not accommodate an expanded number of logistical units. Therefore, the shuttle system, which has seen significant performance improvements in recent years, proved to be the best solution.
The mechanization concept includes, in addition to the shuttle (used for temporary storage and sorting), automated unloading, semi-automatic loading of roll containers—with a robotic pilot in development—and a pick-to-light system. Automated roll container transport via AMRs (autonomous mobile robots) and automated guided vehicle systems are also currently being explored.
Our consultants support the end-to-end transition of the implementation.
Program and Project Management
This includes program and project management for the mechanization: providing both substantive and project-based guidance, and preparing decision-making processes in steering committees. We set up a project organization with functional staff and line managers with ultimate responsibility, using standardized reporting formats and project charters to define sub-projects. One of the pitfalls identified was that, while the mechanization could be completed on time, the increased inventory availability might still not be achieved. To ensure this goal was met, it was necessary to also make progress in supply chain management. Together with the CFO, we translated the strategy into requirements for supply chain management in terms of ordering, long- and short-term planning, required competencies, and tools.
Selecting, designing and implementing a new warehouse management system
Increasing inventory availability in stores also required replacing the IT system. The existing system included warehouse management functionality. Supply Today supported Zeeman's management in selecting the new WMS (Warehouse Management System). This system needed to manage the new mechanization and handle both the new and existing item structures during the transition. Our WMS expert provided both technical and project-based guidance for the WMS design.
Facility Upgrades
A consequence of choosing the shuttle system was the need to raise the roof of one of the distribution center's halls and implement new provisions, such as electrical installation, a new sprinkler system, and water supplies. Additionally, the current floor was unsuitable for the shuttle load, and mezzanines required precise placement. Our architect and construction supervisor coordinated this process, providing both substantive and project-based oversight.