Hessing Supervers
Design layout of production facility
2 min leestijdDevelopment of various production and logistics layouts to facilitate the growth and integration of multiple production sites for Hessing Supervers.
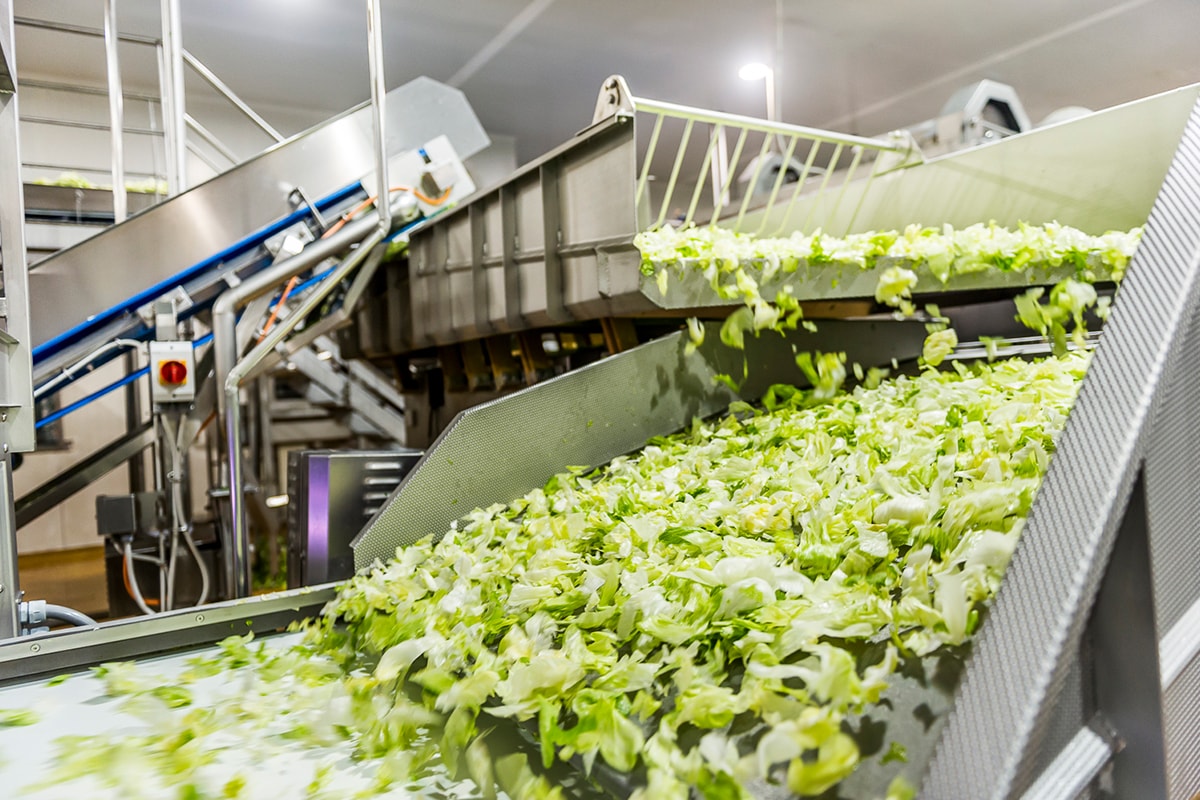
Hessing is the market leader in cutting fresh vegetables and producing meal salads. The company has multiple production sites, with the largest located in Zwaagdijk and Helmond. Previous studies indicated that substantial benefits could be achieved by restructuring the production and logistics infrastructure. The starting point was the management's desire to develop an optimal layout for their production sites, initially considering an expansion in Zwaagdijk.
Impact of Growth on Space Requirements for Production Capacity
First, a clear understanding of the impact of growth had to be developed: in which segments is growth expected? On which production resources will these products be produced? What does the growth mean for each part of the production capacity? All production capacities were mapped out. This led to some discussion about the impact of a different setup with more space on capacity. Through thorough analysis by a Hessing team, it was possible to determine where future bottlenecks in production would arise and what expansion would be necessary.
Each (new) production resource was initially assigned a floor area, which could change depending on the setup and any innovations or optimizations in the flows. Innovations mainly involve improvements to the production process due to new insights or advancements in technology.
Another question was to determine what synergy benefits could be achieved by relocating parts of the production from one site to another.
Significant reduction in movements
With various scenarios for the forecasted production capacity, the associated space requirements, and the relocation of part of the production as starting points, we could then begin designing layout options. The first step was to map the current situation. As in most production environments, after several years, significant benefits can be achieved by designing a new layout. In this case as well, there were oversized buffer locations, crossing flows, and unnecessarily long routes.
In the design phase, we initially assumed a greenfield situation: an optimal routing without considering existing constraints of the building and the supply and access routes. Together with management, production, and logistics stakeholders, various options were developed that closely approximated the greenfield situation.
In our final design, significant savings were realized by greatly reducing movements within production and the warehouse. Additionally, mechanization was found to be possible in certain areas, and business cases were identified, such as for a mechanized warehouse for intermediate storage and for palletizing end-product boxes.