Dillewijn Zwapak
Newly built mechanised logistics operation
2 min leestijdIntegration of three sites on a newly developed mechanised logistics operation for the merged Dillewijn Zwapak
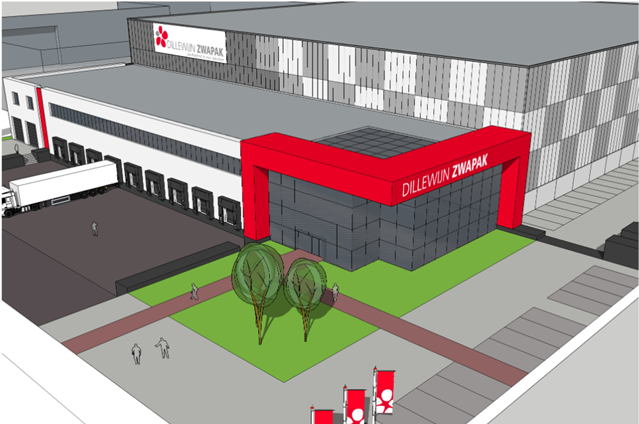
Dillewijn Zwapak is an international company with branches in several countries and is part of the Van Dillewijn Group.
Dillewijn Zwapak's head office is located in Amstelveen in the Netherlands. From there it serves growers, exporters, wholesalers and retail chains. Retailers can visit the cash & carries at the flower auctions in Aalsmeer, Ede, Eelde and Naaldwijk or the webshop.
Dillewijn Zwapak offers a wide range of standard packaging products such as (un)printed sleeves, foils and bouquet holders. The range also offers a wide selection of floristry items such as scissors, flower food, binding wire, decorative materials and floral foam.
Original situation and demand
After merging Dillewijn and Zwapak, the logistics operation had to be optimised. Running the logistics operation at three locations was very inefficient and entailed high handling and storage costs.
Our brief:
What is the most optimal logistics solution for Dillewijn Zwapak, taking into account the desired growth and quality improvement.
The options examined are:
1) Expand at one of the 3 locations currently in use
2) Outsourcing to logistics service provider
3) New construction (groene weide)
Preliminary conclusion
The study showed that expansion at one of the three sites would not yield sufficient expansion, which was precisely what Dillewijn Zwapak wanted. The optimum logistics situation could not be achieved there and planning also proved technically unfeasible. The ‘shop’ could not be closed for six months and phased implementation was not an option either.
Continued study
Compare between outsourcing v/d logistics or new construction (on groene weide).
Outsourcing with a logistics service provider
In the past, we have also participated in tender projects for logistics service provider, such as Simon Loos and Bakker Logistiek. There, a lot of insight was gained into the budgeting of such a disbursement project. The overall costs would go down significantly compared to the current situation.
New construction on groene weide
By opting for a ‘groene weide concept’, all requirements and wishes could be met below. Such as the possibility of mechanising / automating partial processes as much as possible. The building is fully tailored to the logistics requirements / conditions, which allowed maximum efficiency to be achieved.
Chosen concept:
- Building 20m high;
- Narrow-aisle storage system with deployment of unmanned combination trucks (AGVs) for pallet entry and exit;
- Deployment of unmanned forklift trucks in the front area and transport to storage. At night, orders were picked by the AGVs and prepared at the dock;
- Man-operated high-order picking trucks in a limited part of the storage area for picking collies;
- 3 platform lifts for efficient storage and order picking of small goods (goods-to-man system).
Conclusion
New construction containing a highly efficient logistics process proved to be the most optimal logistics, both in terms of operational costs, but also in significantly improved quality towards the customer.
Particularly because of the expansion with e-commerce activities, this was fully guaranteed in the new DC, partly due to the 24-hour operation.