Hessing Supervers
Ontwerp lay-out productielocatie
2 min leestijdOntwikkeling van verschillende productie- en logistieke lay-outs om de groei en integratie van productielocaties van Hessing Supervers te faciliteren
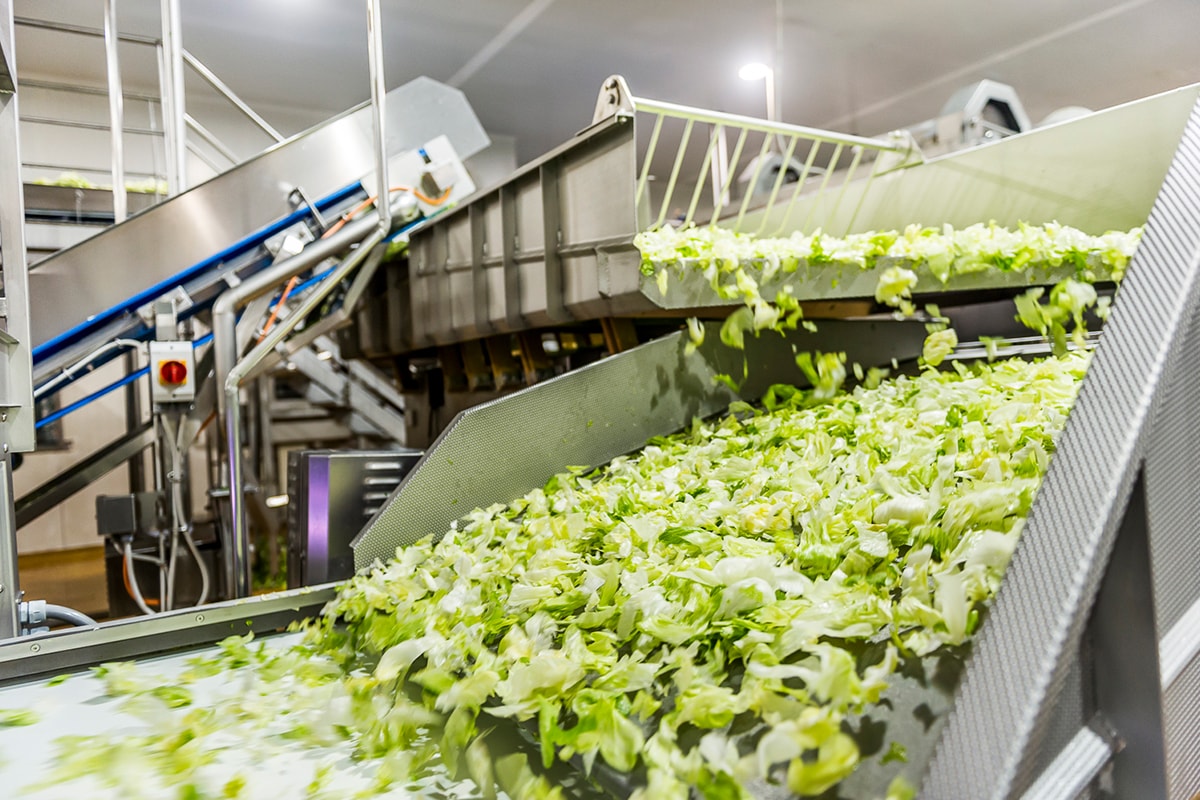
Samenvatting
Hessing is marktleider in het snijden van verse groenten en het produceren van maaltijdsalades. De onderneming heeft meerdere productielocaties waarvan de grootste zijn gevestigd in Zwaagdijk en Helmond. In eerdere studies was aangetoond dat substantiële voordelen te behalen waren in het herinrichten van de productie-en logistieke infrastructuur. Vertrekpunt was de wens van het management een optimale layout te ontwikkelen voor hun productielocaties waarbij toen nog aan een uitbreiding werd gedacht in Zwaagdijk.
Impact van groei en integratie op ruimtebeslag productiecapaciteit
Allereerst moest een duidelijk beeld worden ontwikkeld van de impact van de groei: in welke segmenten wordt groei verwacht. Op welke productiemiddelen wordt deze producten geproduceerd. Wat betekent de groei voor elk onderdeel van de productiecapaciteit. Alle productiecapaciteiten werden in kaart gebracht. Daarbij ontstond enige discussie wat de impact van een andere opstelling met meer ruimte voor impact had op de capaciteit. Door grondige analyse van een team van Hessing kon worden vastgesteld waar toekomstige knelpunten in de productie zouden ontstaan en welke uitbreiding noodzakelijk was.
Aan elk (nieuw) productiemiddel werd een initiële vloermaat verbonden, die kon veranderen afhankelijk van de opstelling en afhankelijk van eventuele innovaties of optimalisatie in de stromen. Innovaties betreft vooral verbeteringen van het productieproces vanwege andere inzichten of verbeterde stand der techniek.
Een andere vraag was om vast te stellen welke synergievoordelen mogelijk waren bij het verplaatsen van delen van de productie van de ene locatie naar de andere.
Greenfield versus uitbreiding bestaande locatie
Met verschillende scenario’s voor de geprognotiseerde productiecapaciteit, het daarbij behorende ruimtebeslag en het verplaatsen van een deel van de productie als als uitgangspunten konden we vervolgens starten met het ontwerpen van de lay-out opties. De eerste stap was het in kaart brengen van de huidige situatie. Zoals in de meeste productieomgevingen is er na enige jaren behoorlijk wat voordeel te behalen indien een nieuwe lay-out kan worden ontworpen. Ook hier was sprake van te grote buffer locaties, kruisende stromen, onnodig lange routes.
Bij het ontwerp gingen we in eerste instantie uit van een greenfield situatie: een optimale routering zonder rekening te houden met bestaande beperkingen van het pand en de aan- en afvoerwegen. Samen met management, productie- en logistieke stakeholders zijn verschillende opties ontwikkeld, die zo dicht mogelijk de greenfield situatie benaderde.
Besparingen door sterke reductie van bewegingen en mechanisering
In ons uiteindelijk ontwerp werden forse besparingen gerealiseerd door sterke reductie van bewegingen in de productie en in het magazijn. Daarnaast bleek ook op onderdelen mechanisatie mogelijk en businesscases aanwezig, zoals voor een gemechaniseerd magazijn voor tussenvoorraden en voor het palletiseren van dozen eindproduct.